Manufacturing
Enjoy the Journey of Silicone Product From Raw Material to Finished Product
Learn how Infaye manage the whole manufacturing process of silicone product and complete your order on budget and on time, batch after batch.
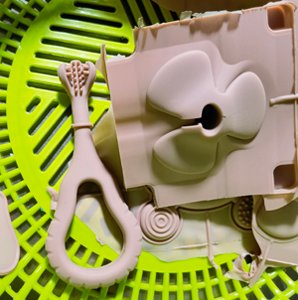
Sampling Prototype

Material Mixing

Bulk Injection

Quality Control

Packaging
Prototype and Molding
CNC machining investment speed up production leadtime
Product Manufacturing Tour Video
Where the world turns bright & colorful
Silicone Molding Products Manufacturing
The Heart of Silica Molding Performance

3D design
OEM/ODM are welcome. experienced engineer teamhave good command of Rhino3D NURBS, and can and finish 3D drawing base on custom’s requirements and provide solutions.
Prototype
Prototype will be made once layout approved and order confirm. Which allow us to provide visibility and realizability physical sample for touching and checking, and we can modify production size and colors for final production
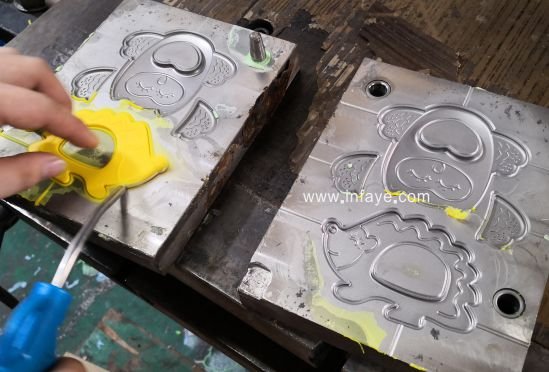

Mold making
We have our own mold tooling facility instead of out-sourcing, as well as skilled workers can speed up and shorten production lead time.
Silicone mixing
- Silicone rubber raw material is milling under suitable material ratio, pressure and time, convert from solid, tough to soft and flexible.

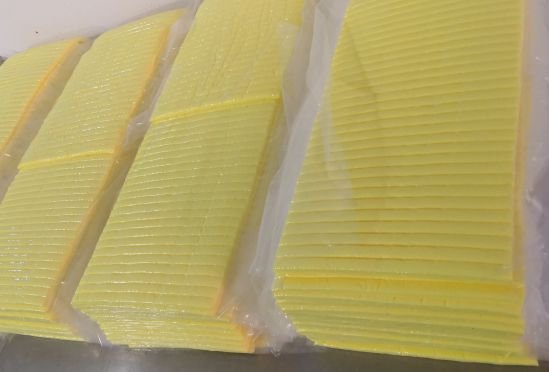
Material Ready
Keep the stripes clean and in place, which is get ready for bulk production
Material cutting
When material flat soft sheet is ready, and it will be cut into many small stripes base on production size & weight, which the stripes can cover into several cavities at one time effectively instead of putting one by one.


Bulk injection
Raw material is injected under suitable temperature, pressure and time, then formed into production by molding .
Oven treatment
All productions will be 100% check and arrange 2nd oven treatment for 6 to 8 hours under 180 to 190 centidegree, which is in order to make our production with enough oven treatment and comply with FDA / LFGB standards.
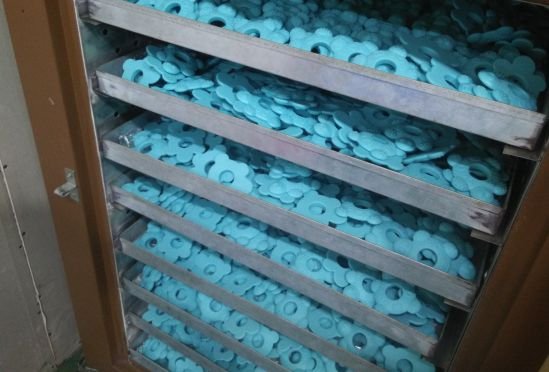

Production trimmed
Because of parting lines, production will have burrs that needs trimming and cutting after injection.
Quality control
The care and attention put into every one of the products we produced. strict quality control plans translate into dimensional layouts, and material certification for durability
We have the full control over our process, from raw material to trimming to finishes
- Incoming checking, for example, material no. And batch
- Inline checking, such as checking product if lack of material, if oven treatment enough
- Final checking including scratch, dirty, broken, flash, etc.
- Production certification: FDA, REACH, BPA, ROHS, etc.


2nd production check
Packing customization
Packing customization:Besides regular polybag packing, we can also provide design for clients’ custom packaging. Such as plastic box, blister, backing card, open box, etc.
